ADC12 (also called A383) is one of the most commonly used materials in die casting. It is a Japanese name for a recycled die-cast aluminum alloy. Known for its excellent casting performance, cost-effectiveness, and mechanical properties, ADC12 is widely used in the automotive industry and daily life.
From this article, you will learn about:
The chemical composition of ADC12
Mechanical properties of ADC12
Why Choose ADC12 for Die Casting
Top Applications of ADC12 Aluminum Alloy
ADC12 vs. Other Aluminum Die-Casting Alloys
Conclusion
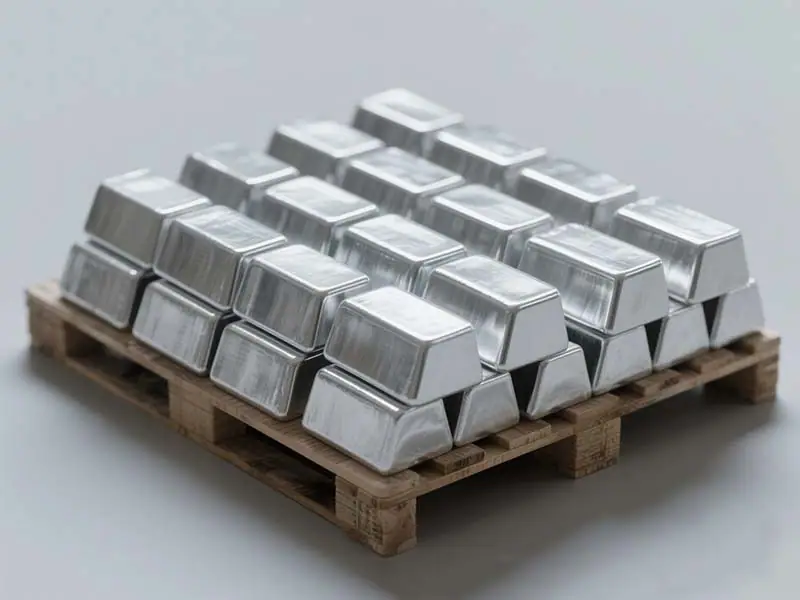
Chemical composition of ADC12
ADC12, a Japanese JIS standard alloy (equivalent to China’s YL113 and the U.S.’s A383), is a high-silicon aluminum alloy specifically designed for high-pressure die casting. Below are its primary specifications:
Element | Composition (%) | Key Role |
---|---|---|
Si (Silicon) | 9.5 – 12.0 | Enhances fluidity, reduces shrinkage, and improves castability. |
Cu (Copper) | 1.5 – 3.5 | Increases strength, hardness, and machinability. |
Fe (Iron) | ≤1.3 | Controls ductility; excess reduces toughness. |
Mg (Magnesium) | ≤0.3 | Balances hardness and mechanical properties. |
Zn (Zinc) | ≤1.0 | Improves corrosion resistance; excess may cause intergranular corrosion. |
Mn (Manganese) | ≤0.5 | Neutralizes iron’s harmful effects and stabilizes high-temperature performance. |
Al (Aluminum) | Balance | Base metal providing lightweight properties and structural integrity. |
Additional Notes
- Impurity Limits: Ni (≤0.5%), Sn (≤0.3%), other impurities (≤0.3% total).
- Key Feature: High silicon content distinguishes ADC12 from alloys like A380 or ADC10, making it ideal for thin-walled, complex die-cast parts.
This table provides a concise reference for engineers and manufacturers working with ADC12 in die-casting applications.
Mechanical properties of ADC12
Below is a horizontal table summarizing the mechanical properties of ADC12 aluminum alloy in English, formatted for clarity and technical documentation:
Property | Value/Description | Testing Standard | Remarks |
---|---|---|---|
Tensile Strength | 230–310 MPa | JIS H 5302 | Suitable for structural components |
Yield Strength (0.2%) | 130–150 MPa | ASTM B557 | Ensures load-bearing capacity |
Elongation at Break | 1–3% | JIS Z 2241 | Limited ductility, typical for die casts |
Hardness (Brinell) | 80–100 HB | ASTM E10 | Balances wear resistance and machinability |
Density | 2.68 g/cm³ | — | Lightweight advantage |
Thermal Conductivity | 96–120 W/m·K | ASTM E1461 | Ideal for heat dissipation applications |
Fatigue Strength | ~90 MPa (at 10⁷ cycles) | ISO 1143 | Suitable for dynamic load environments |
Why Choose ADC12 for Die Casting?
ADC12’s popularity stems from its unique advantages in manufacturing:
- Superior Fluidity: High silicon content ensures seamless filling of intricate molds, reducing defects like porosity.
- Cost Efficiency: Lower melting temperatures save energy and extend mold lifespan.
- Machinability: Minimal tool wear during post-casting processes like drilling or milling.
- Surface Finish: Naturally smooth surfaces reduce the need for secondary polishing.
- Corrosion Resistance: Ideal for parts exposed to moisture or chemicals.
Top Applications of ADC12 Aluminum Alloy
ADC12’s versatility makes it indispensable across industries. Here are its primary uses:
- Automotive Components
- Engine brackets, transmission housings, and cylinder heads.
- Electric vehicle (EV) battery casings and motor housings.
- Why ADC12? Balances lightweight design with structural integrity.
- Electronics & Consumer Goods
- Heat sinks, smartphone frames, and laptop chassis.
- Power tool housings and LED lighting fixtures.
- Why ADC12? Excellent thermal dissipation and EMI shielding.
- Industrial Machinery
- Pump housings, valve bodies, and hydraulic components.
- Why ADC12? Withstands high-pressure environments.
- HVAC Systems
- Compressor parts and heat exchanger components.
- Why ADC12? Corrosion resistance in humid conditions.
ADC12 vs. Other Aluminum Die-Casting Alloys
While ADC12 dominates the market, understanding its differences from alloys like ADC10 or A380 is crucial:
Property | ADC12 | ADC10 | A380 |
---|---|---|---|
Fluidity | Excellent | Good | Moderate |
Machinability | High | Moderate | High |
Cost | Moderate | Low | High |
ADC12 strikes a balance between performance and affordability, making it a go-to for high-volume production.
Sustainability & Compliance
ADC12 aligns with eco-friendly manufacturing trends:
- Recyclability: 95%+ recyclability rate reduces environmental impact.
- RoHS Compliance: Free from restricted hazardous substances.
Conclusion
ADC12 aluminum alloy remains a cornerstone of die-casting industries due to its adaptability, durability, and cost-efficiency. Whether for automotive innovation, electronics miniaturization, or industrial machinery, ADC12 delivers precision and reliability. Manufacturers prioritizing quality and sustainability continue to favor this alloy for next-generation applications.