With fast economic growth, industries like cars, communication equipment, trains, and machinery are growing quickly. This has made die casting develop fast too. Now, die cast products are more varied and complex, and the need for automation is higher.
For the die casting industry, the quality of castings decides its success. Moving toward high-end die cast products is the future, so stable quality is more important than ever.
In this guide, we will explain:
What is Auto Die Casting?
How die casting automation works?
Why it matters for manufacturing (like cars).
How to pick the right factory for your needs.
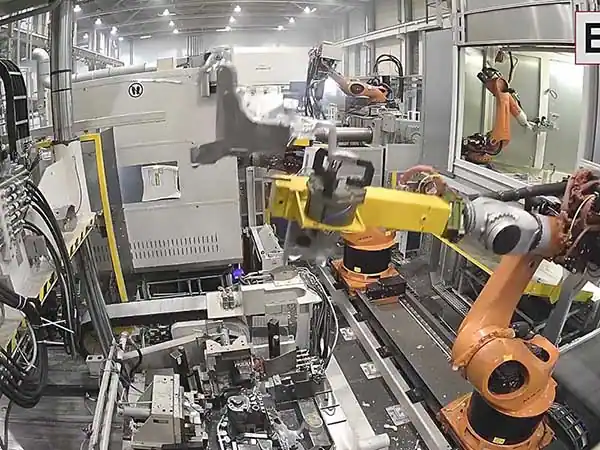
What is Auto Die Casting?
Auto die casting is a manufacturing method where melted metal is poured into a mold under high pressure to create car parts. It’s widely used because it makes parts that are lightweight, strong, and cheap to produce. For example, engine blocks, gearboxes, and even electric vehicle (EV) battery cases are often made this way.
Die-casting automation involves related processes such as spray, part removal, deburring, deburring, and cleaning
How Does Auto Die Casting Work?
The auto die casting process has four simple steps:
Step 1: Melt the Metal
Metals like aluminum, zinc, or magnesium are heated until they turn into liquid.
Step 2: Inject Liquid into a Mold
The liquid metal is pushed into a steel mold at high pressure. This ensures the metal fills every part of the mold.
Step 3: Cool and Remove the Part
After a few seconds, the metal cools down and hardens. The mold opens, and the part is taken out.
Step 4: Trim and Finish
Extra metal (like flash or sprues) is cut off, and the part is polished or coated if needed.
Why Use Die Casting for Cars?
Here are four reasons why car makers love die casting:
3.1 Saves Money
- Fast production (thousands of parts per day).
- Less material waste compared to machining.
3.2 Strong & Lightweight
- Lighter parts improve fuel efficiency.
- Metals like aluminum are strong but weigh 60% less than steel.
3.3 Smooth Surface
- Parts come out shiny and smooth, reducing polishing work.
3.4 Complex Shapes
- Can make detailed parts like engine blocks or thin-walled housings.
Common Car Parts Made by Die Casting
- Engine parts: Pistons, cylinders, and oil pans.
- Transmission components: Gearboxes and clutch housings.
- Brackets and housings: Sensor mounts, wheel hubs.
- EV battery cases: Lightweight frames to hold battery cells.
Best Metals for Auto Die Casting
Metal | Benefits | Used For |
---|---|---|
Aluminum | Light, resists rust, cheap | Engine parts, EV cases |
Zinc | Strong, easy to cast | Door handles, small gears |
Magnesium | Super lightweight (30% lighter than aluminum) | EV components |
5 Tips to Pick a Good Die Casting Factory
- Experience with car parts: Ask for examples of past projects.
- Quality certifications: Look for ISO 9001 or IATF 16949.
- Mold design support: Good factories help design molds to save costs.
- Compare prices and speed: Avoid factories with hidden fees or slow delivery.
- Read reviews: Check Google or industry forums for feedback.
Problems in Auto Die Casting (and Fixes)
- Porosity (air bubbles): Use vacuum die casting to remove trapped air.
- Cracks: Improve mold cooling to reduce stress.
- Dimensional errors: Check and repair molds regularly.
Future of Auto Die Casting
- Robots: Faster production with automated trimming and quality checks.
- Recycling: Reuse 90% of metal scraps to cut costs and pollution.
- New alloys: Stronger metals for electric cars and self-driving tech.
Conclusion
Auto die casting helps car makers create better parts at lower costs. To get the best results, choose a factory with experience, modern machines, and a focus on quality.
FAQ
Q1: Is die casting cheaper than machining?
Yes! Die casting makes thousands of parts fast, reducing labor and material costs.
Q2: Which metal is best for car parts?
Aluminum is the most popular because it’s lightweight and strong.
Q3: Can die casting make very thin parts?
Yes, it can make walls as thin as 1-2 millimeters.
Q4: How long does a die casting mold last?
A steel mold can make 100,000 to 1 million parts, depending on the metal used.
Q5: Why do some parts have air bubbles?
Air gets trapped during injection. Vacuum die casting solves this problem.