Metal fabrication is the backbone of modern manufacturing, and choosing the right cutting method can make or break a project. Two of the most common techniques are laser cutting and metal stamping. Whether you’re working with a steel sheet, producing intricate laser cutting metal parts, or managing high-volume production using a sheet metal stamping machine, selecting the right process is critical. This article offers a technical comparison to help engineers and manufacturers decide between laser cutting and stamping based on quality, cost, flexibility, and lead time.
Understanding the Basics of Laser Cutting and Stamping
What Is Laser Cutting?
Laser cutting uses a high-powered laser for cutting steel and other metals with precision. It’s a non-contact process ideal for thin to medium materials, offering exceptional accuracy with minimal heat-affected zones. Modern sheetmetal laser cutting systems are programmable via CAD/CAM software, making them perfect for prototyping or producing custom laser cut sheet metal. In some cases, pliers for cutting metal may be used post-process to trim or adjust fine features manually.
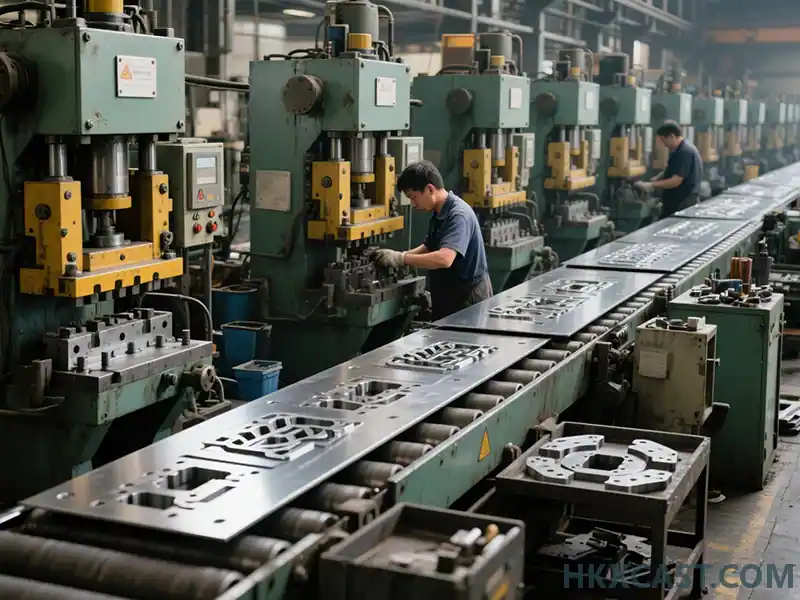
What Is Metal Stamping?
Metal stamping uses dies and a metal stamp press machine to form or punch metal sheets into shape. It is widely used in steel sheet stamping applications, particularly in the automotive and appliance industries. For high-strength or specialized applications, high-temperature metal stamping enables shaping of heat-resistant alloys. This process is optimal for mass production, especially when tooling is done via a sheet metal stamping machine for consistency and throughput.
Head-to-Head Comparison: Laser Cutting vs. Stamping
Quality Comparison Table
Feature | Laser Cutting | Stamping/Punching | Remarks |
---|---|---|---|
Workpiece Deformation | No | Yes | Non-contact laser process applies no physical force |
Tool Wear | No | Yes | Stamping tools degrade over time |
Tool Replacement Needed | No | Yes | Dies require periodic replacement |
Material Hardness | Cuts all hardness levels | Requires calculations | Stamping harder metals needs stronger tooling |
Post-Cut Polishing Needed | No | Yes | Laser edges are smooth and clean |
Complex Structure Processing | Handles intricate designs without molds | Limited flexibility | Lasers are mold-free, enabling faster iterations |
Quality | 0.1mm (meets CIMC Silver Green standard) | mm-level precision | Laser is 10x more precise |
Processing Time | Standard | 10x longer | Laser is faster for small to mid-scale runs |
Lead Time | Immediate | Long (mold making, logistics) | Mold cost and wait time add delays |
Precision and Tolerances
Laser cutting delivers ultra-clean edges and tight tolerances—particularly important when working with laser cut sheet steel or lightweight enclosures. In contrast, stamping precision relies on die quality and press accuracy. For one-off or short-run parts like laser cutting metal parts, laser is often the more efficient and accurate choice.
Speed and Production Volume
When high volume is the goal, stamping dominates. It allows fast cycling on a metal stamp press machine, making it ideal for thousands of identical parts. However, sheet metal cutting laser systems are excellent for low to mid-range production, where frequent design changes or small batches are required. When both cutting and forming are needed, sheet metal laser cutting and bending can combine operations in a seamless digital workflow.
Tooling, Setup, and Flexibility
Tooling and Setup Costs
Stamping requires expensive tooling and long lead times—each part variation may need new dies. In contrast, custom laser cut sheet metal needs no hard tooling, making it ideal for agile development and one-off projects.
Material Utilization and Waste
Laser cutting excels in nesting and efficient use of raw material, minimizing scrap in laser cutting metals operations. While stamping can also be efficient at scale, early-stage trim and misalignment waste can occur, especially during setup. That said, one of the major advantages of metal stamping is that, once running, it produces parts consistently with minimal variation.
Design Flexibility and Prototyping
Need to modify a bracket dimension? With sheetmetal laser cutting, just update the CAD file and rerun. This kind of agility is impossible with stamping unless you invest in new tooling. That’s why industries like electronics, aerospace, and startup hardware manufacturing lean heavily on laser processes during development.
Maintenance and Operational Considerations
Laser systems require routine lens cleaning, software updates, and calibration. Stamping systems, on the other hand, involve physical maintenance—die sharpening, press tuning, and tooling changes. Post-processing steps such as folding may involve tools like a metal brake cutter, which is often used in both stamping and laser workflows to create final geometries from steel sheet components.
Use Case Scenarios: When to Choose What
Choose Laser Cutting When:
- You need flexible, fast prototyping
- Design changes are frequent
- You’re producing under 1,000 units
- Working on intricate custom laser cut sheet metal geometries
Choose Metal Stamping When:
- You need to produce thousands to millions of identical parts
- Setup cost is justified by volume
- You’re working with pre-hardened materials for high-temperature metal stamping
Even after cutting or stamping, a metal brake cutter may be used for final bending or edge forming steps.
Process Comparison Table
Category | Traditional Stamping | Laser Cutting |
---|---|---|
Method | Mechanical cutting or punching (requires molds, high waste) | High-density energy focused on small, precise areas |
Tooling | Requires 10–100+ molds per product | No hard tooling required |
Efficiency | Low for prototypes; high for stable designs | High for all volumes |
Cost | High (mold investment, maintenance) | Low (minimal setup cost) |
Flexibility | Low — limited by tooling | High — change CAD, hit “cut” |
Cost Comparison: Short-Term vs Long-Term ROI
- Laser cutting is more cost-effective for volumes under 1,000 parts.
- Stamping becomes more economical when volumes exceed 5,000 units.
- Companies manufacturing steel sheet stamping products often use laser for prototype approval, then transition to stamping for mass production.
Expert Insights and Industry Trends
As manufacturing becomes more digitized, hybrid workflows are on the rise. Many engineers now prototype with sheet metal cutting laser systems and shift to stamping once designs stabilize. The growing use of steel sheet laser cutting machines is driven by faster speeds and automated nesting software. Meanwhile, high-temperature metal stamping remains critical for performance materials in automotive and aerospace.
Conclusion: Which Method Wins?
There’s no absolute winner—each method has its advantages. For agile, short-run production and design freedom, sheetmetal laser cutting is hard to beat. For high-volume, cost-sensitive manufacturing, metal stamping remains the standard. Ultimately, the best process depends on your product lifecycle, material, and scale.
FAQs
1. Which is cheaper: laser cutting or stamping?
Laser cutting is cheaper for small runs. Stamping is cost-effective at high volumes.
2. Can laser cutting replace stamping entirely?
Not entirely. Each method serves different production needs.
3. When does stamping become economical?
Usually around 1,000–5,000 parts and above.
4. Are hybrid methods used in practice?
Yes. Many companies prototype with lasers and scale with stamping.
5. Which is better for steel or aluminum sheets?
Both work well, but a steel sheet laser cutting machine offers more flexibility in thickness and precision.