Introduction
Low pressure die casting is a highly advanced metal forming process that has become indispensable in modern manufacturing. Unlike traditional gravity or high-pressure casting methods, low pressure die casting involves injecting molten metal into a mold under controlled, low-pressure conditions. This technique offers significant advantages in terms of product quality, efficiency, and versatility. In this article, we will delve into the detailed process of low pressure die casting, its key technologies, and its wide-ranging applications across various industries. Additionally, we will explore the benefits, challenges, and future trends shaping this dynamic field.
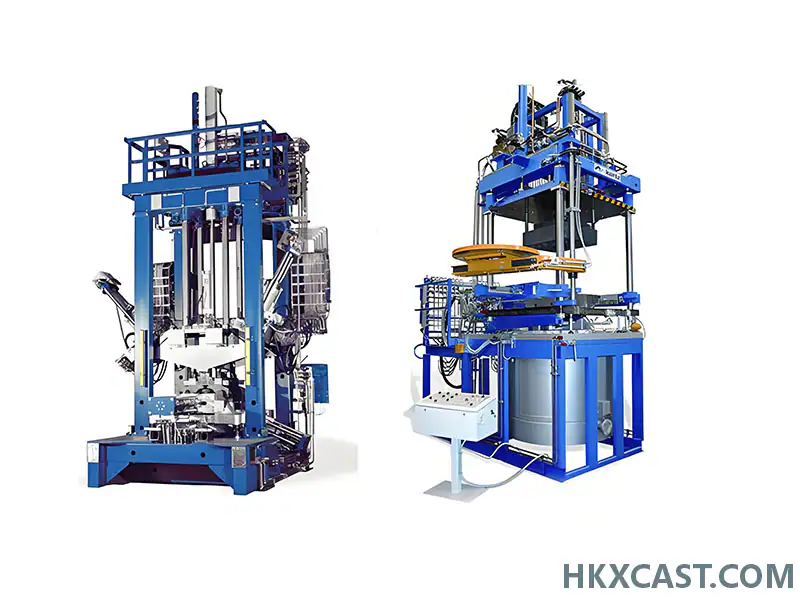
Low-pressure casting machine
The Basic Principle of Low Pressure Die Casting
The core principle of low pressure die casting lies in its ability to inject molten metal into a mold at pressures typically ranging from 0.5 to 1.5 bar. This low-pressure environment minimizes gas entrapment, reduces porosity, and enhances the density and surface finish of the castings. Compared to gravity casting, where metal flows under the force of gravity, low pressure die casting ensures a more controlled and uniform filling of the mold cavity.
Key Advantages of Low Pressure Die Casting:
- Improved Density: The low-pressure environment reduces the formation of air pockets and voids, resulting in denser, higher-quality castings.
- Enhanced Surface Quality: Castings produced through low pressure die casting exhibit smoother surfaces, often eliminating the need for extensive post-processing.
- Material Savings: Precise control over the injection process minimizes material wastage.
- Energy Efficiency: Low pressure die casting consumes less energy compared to high-pressure methods, making it more environmentally friendly.
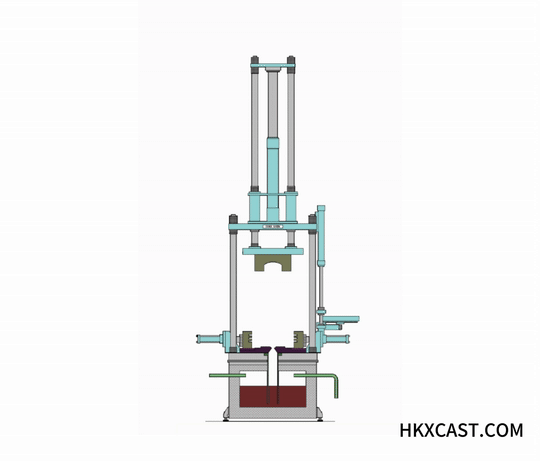
Low-pressure-casting-production-process
The Detailed Process of Low Pressure Die Casting
The low pressure die casting process consists of several critical steps:
Step 1: Preparation
- Mold Design and Manufacturing: The mold is designed based on the specific requirements of the final product, ensuring optimal structural integrity and ease of demolding.
- Material Selection: Common materials used include aluminum alloys and magnesium alloys, which offer excellent flow properties and lightweight characteristics.
- Temperature Control: Melting furnaces and holding furnaces are used to maintain precise temperatures, ensuring the metal remains fluid and suitable for casting.
Step 2: Low Pressure Injection
- Pressure Control: A low-pressure pump is used to inject molten metal into the mold at pressures between 0.5 and 1.5 bar. This controlled pressure ensures smooth and even filling of the mold cavity.
- Injection Speed: The speed of injection is carefully adjusted to prevent oxidation and ensure proper filling without cold shuts.
Step 3: Cooling and Solidification
- Cooling System: The mold incorporates cooling channels to facilitate uniform heat dissipation, reducing thermal stress and deformation during solidification.
- Solidification Process: By controlling the cooling rate, defects such as shrinkage and warping can be minimized.
Step 4: Demolding and Post-Processing
- Demolding: Once the casting has cooled sufficiently, it is removed from the mold using specialized tools.
- Post-Processing: The casting may undergo finishing operations such as grinding, polishing, or machining to meet final product specifications.
Key Equipment and Technologies in Low Pressure Die Casting
Effective implementation of low pressure die casting relies heavily on advanced equipment and cutting-edge technologies.
Primary Equipment
- Low Pressure Die Casting Machines: These machines provide the necessary low-pressure environment to inject molten metal into the mold.
- Melting Furnaces and Holding Furnaces: Used to melt and maintain the temperature of the metal, ensuring optimal fluidity.
- Temperature Control Systems: Precisely regulate the temperature throughout the process to achieve consistent results.
- Automation Control Systems: Monitor and adjust process parameters in real-time, enhancing efficiency and accuracy.
Critical Technologies
- Digital Simulation: Computer-aided simulation helps optimize the pouring path and pressure distribution。
- Mold Design: Advanced CAD/CAE technologies ensure molds are durable and accurate.
- Pressure and Temperature Control: Sensors and controllers enable precise regulation of these critical parameters.
Applications of Low Pressure Die Casting
Low pressure die casting finds extensive use across multiple industries due to its ability to produce high-quality, complex parts with precision.
Automotive Industry
- Engine Components: Cylinder blocks and cylinder heads require high strength and heat resistance, making low pressure die casting an ideal choice.
- Chassis Components: Suspension arms and steering knuckles benefit from the process’s ability to create strong, lightweight parts.
- Exterior Parts: Wheels, bumper brackets, and other exterior components demand both aesthetics and durability, which low pressure die casting delivers.
Aerospace Industry
- Structural Components: Airframe frames and engine parts require precision and high strength, making low pressure die casting a preferred method.
- Lightweight Components: The aerospace industry prioritizes weight reduction without compromising performance, a capability well-suited to low pressure die casting.
Electronics and Appliances Industry
- Motor Housing: Electronics components like motor housings require good thermal conductivity and insulation properties.
- Communication Device Enclosures: Lightweight yet robust enclosures for communication devices are efficiently produced using low pressure die casting.
Building and Hardware Industry
- Window Frames: Lightweight and corrosion-resistant window frames are commonly manufactured using this process.
- Locks and Hinges: Precision-engineered hardware components benefit from the high dimensional accuracy of low pressure die casting.
Advantages and Challenges of Low Pressure Die Casting
Advantages
- High Precision: The controlled low-pressure environment ensures consistent dimensions and superior surface quality.
- Low Scrap Rate: Through precise process control, waste is significantly reduced, leading to cost savings.
- Suitability for Complex Shapes: Low pressure die casting excels at producing intricate geometries with high fidelity.
- Ease of Automation: The process is amenable to automation, enabling efficient mass production.
Challenges
- High Initial Investment: The machinery and equipment required for low pressure die casting can be expensive, particularly for large-scale industrial setups.
- Complex Mold Design: Developing molds for low pressure die casting demands expertise and careful planning.
- Technical Expertise Required: Operating and maintaining the process necessitates skilled personnel familiar with intricate process parameters and equipment operation。
Future Trends
As technology advances and market demands evolve, low pressure die casting is poised for continued innovation and growth.
Automation and Intelligence
- AI Integration: Artificial intelligence is being leveraged to optimize process parameters, improving efficiency and product quality.
- Automated Production Lines: Fully automated systems are being developed to minimize human intervention and maximize throughput.
Sustainability and Environmental Focus
- Energy Efficiency: New heating and cooling technologies are being implemented to reduce energy consumption.
- Recyclable Materials: There is a growing emphasis on using recyclable metals to minimize environmental impact.
New Material Development
- Advanced Alloys: Research is ongoing to develop high-performance alloys that meet diverse industry needs.
- Composite Materials: Exploring the potential of low pressure die casting for composite materials is a promising area of development.
Conclusion
Low pressure die casting stands out as a transformative technology in modern manufacturing, offering unparalleled precision, efficiency, and adaptability. While it requires substantial initial investment and technical expertise, the benefits it provides—such as improved product quality, reduced waste, and enhanced sustainability—are undeniable. As industries continue to embrace digitalization and sustainability, low pressure die casting will play an increasingly vital role in shaping the future of manufacturing.
Frequently Asked Questions (FAQ)
Q1: What materials are commonly used in low pressure die casting?
A1: Aluminum alloys and magnesium alloys are widely used due to their excellent flow properties and lightweight characteristics.
Q2: How does low pressure die casting differ from high-pressure die casting?
A2: Low pressure die casting operates at pressures between 0.5 and 1.5 bar, while high-pressure die casting can reach tens or even hundreds of atmospheres. Low pressure die casting is better suited for complex shapes, whereas high-pressure die casting excels in achieving high density and strength.
Q3: What is the typical pressure range for low pressure die casting?
A3: The typical pressure range for low pressure die casting is 0.5 to 1.5 bar, though this can vary depending on the complexity of the casting and the material used.
Q4: What are the main advantages of low pressure die casting?
A4: Low pressure die casting offers improved casting density, enhanced surface quality, lower scrap rates, and reduced material waste.
Q5: How can common defects in low pressure die casting be avoided?
A5: Defects such as porosity and shrinkage can be mitigated through optimized mold design, controlled injection speeds, and precise pressure management.