The manufacturing landscape employs diverse techniques to shape metals, balancing precision, strength, and efficiency. Casting methods like die casting (high-pressure injection into reusable molds) and sand casting (low-cost, expendable sand molds) cater to volume and size needs. Investment casting achieves intricate designs via wax patterns, while lost foam and centrifugal casting enhance efficiency and material integrity. Forging (die/drop) strengthens metals via compression, refining microstructure. Rolling (hot/cold) forms sheets/bars via rollers. Modern additive methods (SLM/SLS) enable complex geometries via laser-fused powders. Metal injection molding merges powder metallurgy with injection principles for small, precise parts. Stamping, drawing, and squeeze casting optimize sheet/semi-solid forming. Processes like continuous casting and roll forming streamline mass production, while grinding and machining (turning/milling) ensure precision. Innovations like metal deposition and die-cutting expand repair and shaping capabilities. Each technique addresses unique demands, driving advancements in aerospace, automotive, and industrial sectors.
1.Die casting
Die casting (note: die casting is not short for pressure casting) is a metal casting process. It uses high pressure to force molten metal into a mold cavity. The molds are usually made from stronger metal alloys. This process is similar to plastic injection molding.
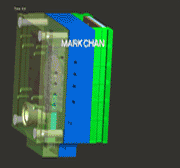
2.Sand casting
Sand casting(Also known as Expandable casting) uses sand to create the mold. A pattern (a model of the final part, often made of wood) is placed in sand, and sand is packed around it. After removing the pattern, the sand keeps the shape of the mold.
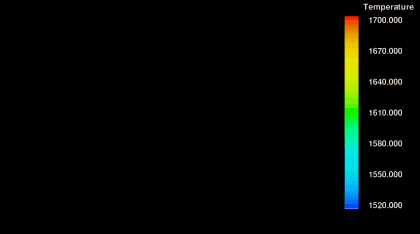
To remove the pattern before pouring metal, the mold must be made in two or more parts. The mold must have holes for pouring metal and vents for air to escape. After pouring, the metal cools and hardens. Once the part is removed, the mold is destroyed, so a new mold must be made for each part.
3.Investment casting
Investment casting, also called lost-wax casting(It is also a kind of Expandable casting process),, involves making a wax model of the part. The wax is coated with clay to form a mold. After drying, the mold is heated to melt the wax, leaving a hollow ceramic mold. Molten metal is poured into the mold, and once cooled, the final part is formed.
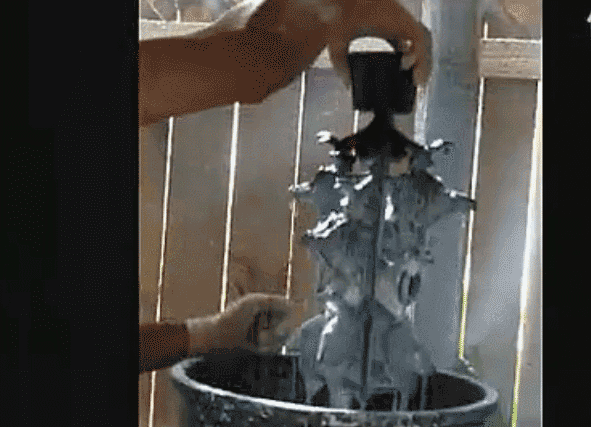
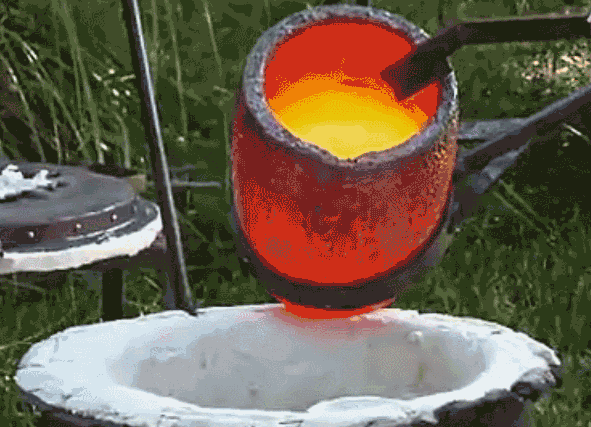
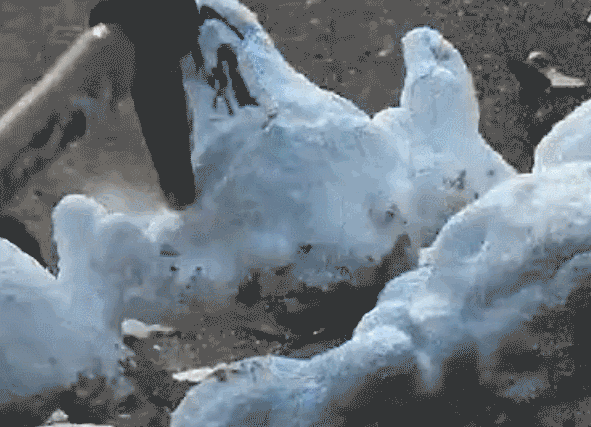
4.Die forging
Drop forging is a metal shaping process where a hammer or press forces metal into a die (mold). This method produces strong, precise parts.
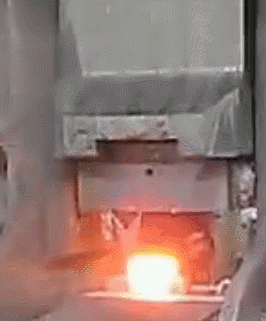
5.Forging
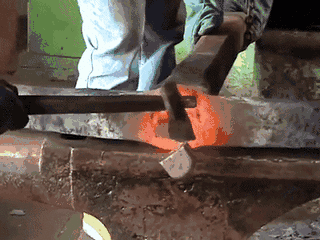
Forging is a processing method that uses forging machinery to apply pressure to metal billets, causing them to undergo plastic deformation to obtain forgings with certain mechanical properties, shapes and sizes. It is one of the two major components of forging and stamping. Forging can eliminate defects such as casting porosity produced during the smelting process of metals, optimize the microstructure, and at the same time, due to the preservation of complete metal flow lines, the mechanical properties of forgings are generally better than those of castings made of the same material. In related machinery, for important parts with high loads and severe working conditions, except for those with relatively simple shapes which can be made of rolled plates, sections or welded parts, forgings are mostly used.
6.Rolling
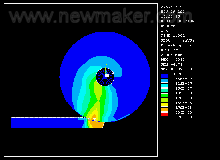
Rolling, also known as calendering, refers to the process of shaping metal ingots through a pair of rollers. If the temperature of the metal exceeds its recrystallization temperature during rolling, this process is called “hot rolling”; otherwise, it is called “cold rolling”. Rolling is the most commonly used method in metal processing.
7.pressure casting
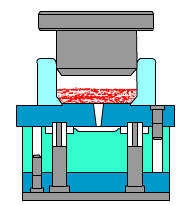
The essence of pressure casting is to fill the cavity of a die casting mold (die casting mold) at a high speed under high pressure, and then form and solidify under pressure to obtain a casting.
8.Low-pressure casting
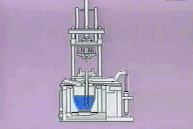
Low-pressure casting is a casting method in which liquid metal fills a mold and solidifies into a casting under the action of low-pressure gas. Low-pressure casting was initially mainly used in the production of aluminum alloy castings. Later, its applications were further expanded to produce copper castings, iron castings and steel castings with high melting points.
9.Centrifugal casting
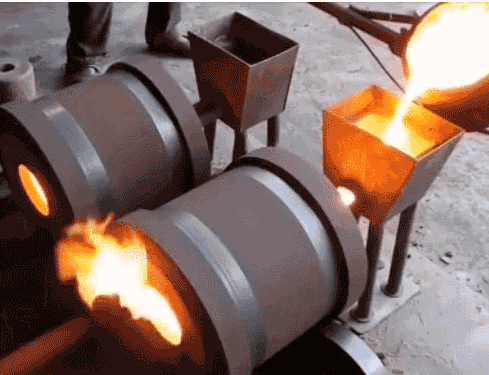
Centrifugal casting is a technique and method that involves injecting liquid metal into a high-speed rotating mold, allowing the molten metal to fill the mold and form a casting under the action of centrifugal force. The molds used in centrifugal casting can be non-metallic molds (such as sand molds, shell molds or investment shell molds), metallic molds or molds with a coating layer or resin sand layer applied inside the metallic mold, depending on the shape, size and production batch of the casting.
10.Lost foam casting
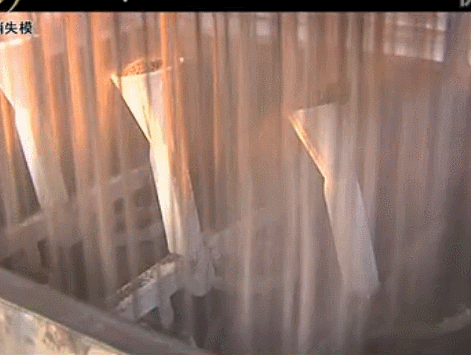
Lost foam casting is a new casting method in which paraffin or foam models similar in size and shape to the casting are bonded and combined into a model cluster, coated with refractory paint and dried, then buried in dry quartz sand and vibrated for molding. Under negative pressure, the casting is poured to vaporize the model, and the liquid metal occupies the position of the model. After solidification and cooling, the casting is formed. Lost foam casting is a new process with nearly no allowance and precise forming. This process does not require mold removal, has no parting surface, and no sand core. Therefore, the castings have no flash, burrs, or draft angles, and reduce dimensional errors caused by core combinations.
11.Squeeze casting
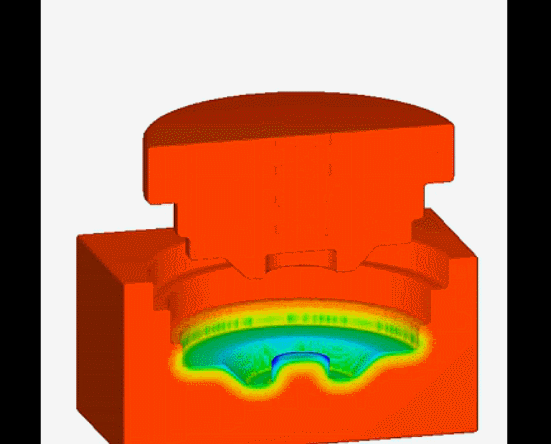
Squeeze casting, also known as liquid die forging, is a method where molten metal or semi-solid alloy is directly injected into an open mold, then the mold is closed to generate filling flow to reach the external shape of the part. Subsequently, high pressure is applied to cause plastic deformation of the already solidified metal (shell), while the non-solidified metal undergoes isostatic pressure and high-pressure solidification simultaneously, and finally the part or blank is obtained. This is direct squeeze casting. Indirect squeeze casting refers to the method where molten metal or semi-solid alloy is injected into the closed cavity of the mold through a punch and high pressure is applied to make it crystallize and solidify under pressure, and finally the part or blank is obtained.
12.Continuous casting
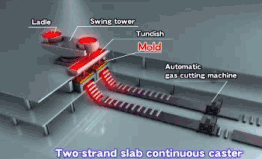
Continuous casting pours molten metal into a mold, cooling it as it moves, producing long metal shapes like bars or sheets.
13.Rabbi
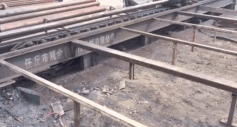
Drawing is a plastic processing method that uses external force to act on the front end of the metal to be drawn, pulling the metal billet out of a mold hole with a cross-section smaller than that of the billet, in order to obtain products with the corresponding shape and size. Since drawing is mostly carried out under cold conditions, it is also called cold drawing or cold pulling.
14.Stamping

Pressing is a forming processing method that uses a press machine and molds to apply external force to plates, strips, tubes and profiles, causing them to undergo plastic deformation or separation, thereby obtaining the required shapes and sizes of workpieces (pressing parts).
15.Metal injection molding
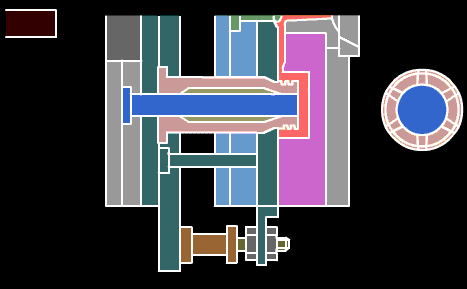
Metal injection molding is a new type of powder metallurgy near-net-shaping technology derived from the plastic injection molding industry. As is well known, the plastic injection molding technology offers low-cost production of various complex-shaped products. However, plastic products have low strength. To improve their performance, metal or ceramic powders can be added to the plastic to obtain products with higher strength and better wear resistance. In recent years, this idea has evolved into maximizing the content of solid particles and completely removing the binder during the subsequent sintering process and densifying the formed part. This new powder metallurgy shaping method is called metal injection molding.
16.Turning processing
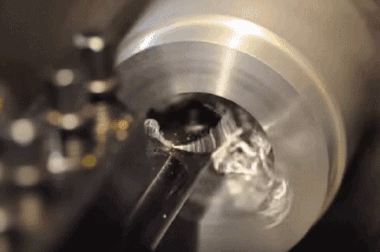
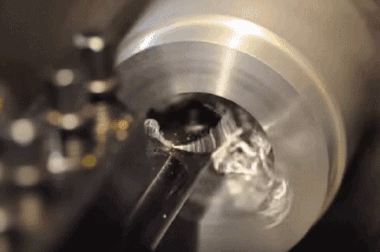
Turning processing refers to the processing carried out by a lathe, which is a part of mechanical processing. The main method of lathe processing is to use a cutting tool to perform turning on a rotating workpiece. Lathes are mainly used for processing shafts, discs, sleeves and other workpieces with rotating surfaces, and are the most widely used type of machine tool processing in mechanical manufacturing and repair factories. Turning processing is a method of cutting the workpiece by rotating the workpiece relative to the tool on the lathe. The cutting force of turning processing is mainly provided by the workpiece rather than the tool.
Turning is the most basic and common cutting processing method, and it holds a very important position in production. Turning is suitable for processing rotating surfaces. Most workpieces with rotating surfaces can be processed by turning methods, such as inner and outer cylindrical surfaces, inner and outer conical surfaces, end faces, grooves, threads and rotating formed surfaces, and the main cutting tools are turning tools.
17.Milling processing
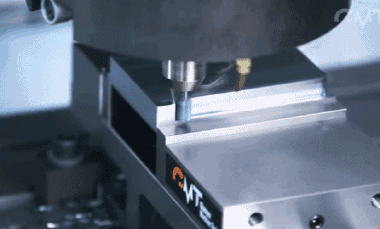

Milling processing involves fixing the workpiece and using a high-speed rotating milling cutter to traverse on the workpiece to cut out the desired shape and features. Traditional milling is mostly used for milling contours and slots and other simple shapes/characteristics. CNC milling machines can perform processing of complex shapes and characteristics. Milling and boring machining centers can perform three-axis or multi-axis milling and boring, used for processing, molds, gauges, jigs, thin-walled complex surfaces, artificial prostheses and blades, etc. When choosing CNC milling processing content, the advantages and key roles of CNC milling machines should be fully exploited.
18.Planing processing
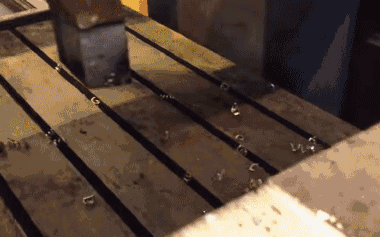
Planing processing is a cutting method where a plane tool performs a horizontal and relatively linear reciprocating motion on the workpiece. It is mainly used for the shape processing of parts. The precision of planing processing is IT9 to IT7, and the surface roughness Ra is 6.3 to 1.6 μm.
19.Grinding processing
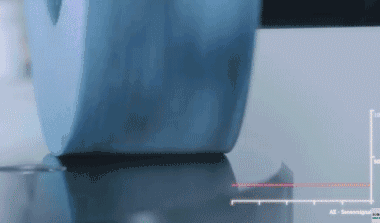
Grinding processing grinding refers to the processing method where abrasive materials and grinding tools are used to remove excess material from the workpiece. Grinding processing is one of the widely used cutting processing methods.
20.Selective laser melting
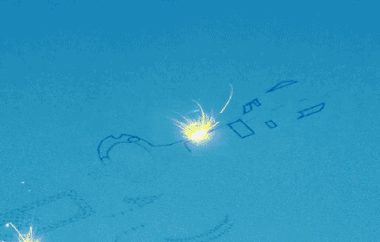
Selective Laser Melting takes place in a trough filled with metal powder. A computer controls a powerful carbon dioxide laser that selectively scans the surface of the metal powder. Where the laser hits, the surface metal powder is completely melted and fused together, while the areas not exposed to the laser remain in a powder state. The entire process takes place in a sealed chamber filled with inert gas.
21.Selective laser sintering
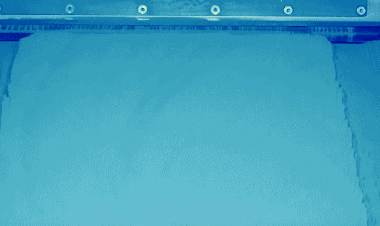
Selective Laser Sintering (SLS) is a method that uses infrared laser as the energy source. The molding materials commonly used are mostly powder materials. During the processing, the powder is first preheated to a temperature slightly below its melting point, and then spread flat under the action of a leveling rod. The laser beam is controlled by a computer to selectively sinter the powder according to the cross-sectional information of each layer. After one layer is completed, the next layer is sintered, and after the entire process is completed, the excess powder is removed, and a sintered part can be obtained. The currently mature processing materials are wax powder and plastic powder. The process of sintering with metal powder or ceramic powder is still under research.
22.Metal deposition
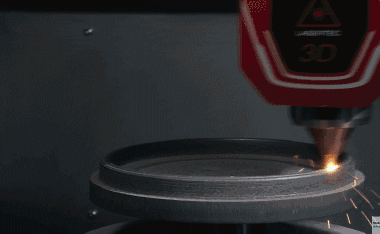
Metal deposition is somewhat similar to the “cream squeezing” type of fused deposition, but it sprays metal powder instead. While the nozzle is ejecting the metal powder material, it also provides high-power laser and inert gas protection simultaneously. This way, it is not limited by the size of the metal powder box, enabling the direct manufacturing of larger-volume components. Moreover, it is also very suitable for repairing precision parts with local damage.
23.Roll forming
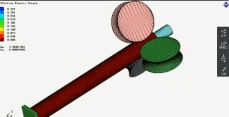
Roll forming is a process that uses a series of consecutive machines to shape stainless steel into complex shapes. The sequence of the rollers is designed in such a way that each machine frame’s roller pattern can continuously deform the metal until the desired final shape is achieved. If the shape of the component is complex, up to thirty-six machine frames can be used, but for simpler shapes, three or four machine frames will suffice.
24.Die-cutting
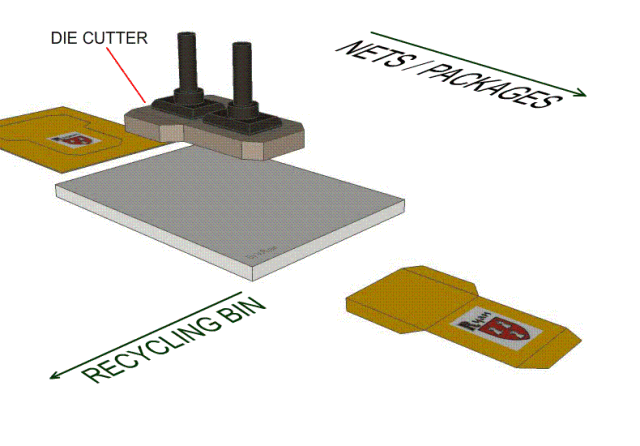
Die-cutting is the material cutting process. After the film is formed in the previous process, it is positioned on the die-cutting die’s master die. The die is closed to remove the excess material, while preserving the 3D shape of the product and matching it with the die cavity.
25.Die-cutting process – Die template
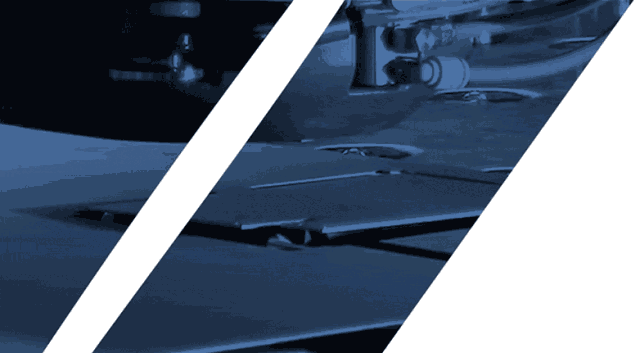
Die-cutting process – Die template, die cutting material processing, positioning the film panel or circuitry on the base plate, fixing the die template on the machine template, using the force provided by the machine pressing to control the blade to cut the material. The difference from punching die cutting lies in that the cut edge is smoother; at the same time, by adjusting the cutting pressure and depth, various effects such as indentations and partial cuts can be achieved through punching. Moreover, the cost of the die is low, and the operation is more convenient, safe and fast.
FAQ: Metal Manufacturing Processes
Q1: What is die casting, and what are its advantages?
A: Die casting injects molten metal into reusable steel molds under high pressure, producing high-precision, smooth-surfaced parts. Advantages include mass production efficiency, dimensional consistency, and suitability for complex shapes (e.g., automotive components).
Q2: How does sand casting differ from die casting?
A: Sand casting uses expendable sand molds for low-cost, low-volume production of large parts (e.g., engine blocks), while die casting employs reusable metal molds for high-volume, intricate designs.
Q3: What is investment casting (lost-wax casting)?
A: Investment casting creates detailed, near-net-shape parts by coating wax patterns with ceramic, melting the wax, and pouring molten metal into the cavity. Ideal for aerospace and jewelry due to high accuracy.
Q4: What are the benefits of forging over casting?
A: Forging compresses metal to enhance strength, eliminate porosity, and improve fatigue resistance. It’s preferred for critical load-bearing parts (e.g., crankshafts) versus castings.
Q5: What distinguishes hot rolling from cold rolling?
A: Hot rolling shapes metal above recrystallization temperatures, improving ductility for sheets/bars. Cold rolling at room temperature increases strength and surface finish (e.g., appliances).
Q6: How does selective laser melting (SLM) work?
A: SLM uses lasers to fuse metal powder layer-by-layer, enabling complex, lightweight geometries (e.g., medical implants) unachievable via traditional methods.
Q7: What is metal injection molding (MIM) used for?
A: MIM combines powdered metal with binders, molded into small, intricate parts (e.g., gears) and sintered for high density. Ideal for high-volume, precision components.
Q8: When is low-pressure casting preferred?
A: Low-pressure casting fills molds slowly with minimal turbulence, reducing defects in aluminum/alloy parts (e.g., wheels), balancing cost and quality.
Q9: What is the role of grinding in manufacturing?
A: Grinding removes material with abrasives to achieve tight tolerances and smooth finishes (e.g., tooling), often as a finishing step after machining.
Q10: How does lost foam casting reduce waste?
A: Lost foam vaporizes polystyrene patterns in sand molds, eliminating parting lines and cores. It minimizes post-processing and material waste for complex designs.