When it comes to welding, two of the most popular methods are MIG (Metal Inert Gas) and TIG (Tungsten Inert Gas). Both techniques have their own strengths and are widely used in various industries. However, choosing between them can be a bit overwhelming, especially for beginners or those new to welding. In this article, we’ll break down the key differences between MIG and TIG welding, helping you decide which method is best suited for your needs.
🔍 Understanding MIG Welding
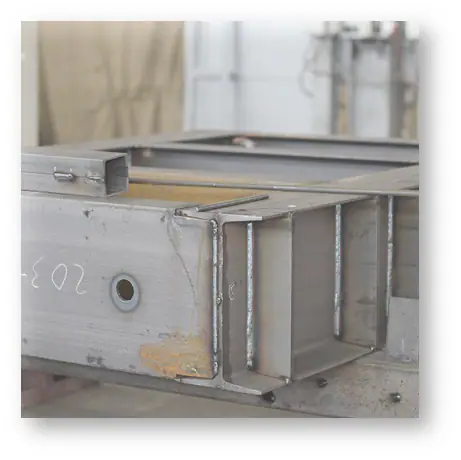
What is MIG Welding?
MIG welding, also known as Gas Metal Arc Welding (GMAW), uses a continuous solid wire electrode that is fed through a welding gun. The process involves an electric arc between the wire and the base material, melting both to create a strong bond. A shielding gas, typically argon or a mix of argon and carbon dioxide, protects the weld from atmospheric contamination.
Key Features of MIG Welding
- Ease of Use: MIG welding is generally considered easier to learn compared to TIG welding. It’s ideal for beginners due to its forgiving nature.
- Speed: MIG welding is faster than TIG welding, making it highly efficient for production environments.
- Versatility: It can be used on a wide range of metals, including steel, aluminum, and stainless steel.
- Cost-Effective: MIG welding equipment tends to be more affordable, and the consumables (wire and gas) are relatively inexpensive.
Ideal Applications
- Automotive Repair: MIG welding is commonly used for repairing car bodies due to its speed and efficiency.
- Construction: It’s great for welding thick metal sheets and structural components.
- Manufacturing: High-volume production often relies on MIG welding for its fast turnaround times.
🔍 Understanding TIG Welding
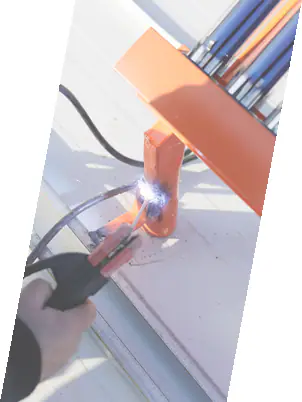
What is TIG Welding?
TIG welding, or Gas Tungsten Arc Welding (GTAW), uses a non-consumable tungsten electrode to produce the weld. Unlike MIG welding, TIG welding requires the welder to manually feed a separate filler rod into the weld pool. A shielding gas, usually pure argon, protects the weld area from oxidation.
Key Features of TIG Welding
- Precision: TIG welding offers exceptional control and precision, making it ideal for intricate and high-quality welds.
- Aesthetic Appeal: TIG welds are clean and visually appealing, with minimal spatter or slag.
- Material Compatibility: While it can be used on many metals, TIG welding excels with thin materials like aluminum, stainless steel, and exotic alloys.
- Skill Requirement: TIG welding demands more skill and practice, making it less forgiving for beginners.
Ideal Applications
- Artistic Projects: TIG welding is favored by artists and craftsmen for creating detailed and precise welds.
- Aerospace and Medical Industries: These sectors require high-quality, defect-free welds, which TIG welding provides.
- Thin-Metal Fabrication: TIG is excellent for welding thin sheets where heat control is critical.
🤔 How to Choose Between MIG and TIG Welding?
Choosing between MIG and TIG welding depends on several factors, including your project requirements, skill level, and available resources. Here’s a breakdown to help you decide:
1. Project Complexity
- Simple, Thick Metals: If you’re working on large, thick pieces of metal, such as automotive panels or construction beams, MIG welding is likely the better choice due to its speed and ease of use.
- Thin, Delicate Materials: For projects involving thin metals or requiring precise, high-quality welds, such as jewelry or aerospace parts, TIG welding is the superior option.
2. Skill Level
- Beginner: If you’re new to welding, MIG welding is more forgiving and easier to master. Its automated wire feed system reduces the learning curve.
- Experienced Welder: For those with advanced skills, TIG welding allows for greater creativity and control, making it perfect for complex projects.
3. Cost Considerations
- Equipment: MIG welding equipment is generally cheaper than TIG welding equipment.
- Consumables: MIG welding wire and gas are less expensive than the filler rods and tungsten electrodes used in TIG welding.
- Time Investment: MIG welding is faster, which can save time and labor costs in production settings.
4. Aesthetics
- Functional Welds: If the appearance of the weld isn’t critical, MIG welding will suffice.
- Professional Finish: For projects where aesthetics matter, such as custom metal art or high-end fabrication, TIG welding is the way to go.
💡 Final Thoughts
Both MIG and TIG welding have their place in the world of metalworking. MIG welding is versatile, fast, and beginner-friendly, making it suitable for a wide range of applications. On the other hand, TIG welding offers unparalleled precision and quality, making it ideal for specialized and high-stakes projects.
Ultimately, the choice between MIG and TIG welding boils down to your specific needs. If you prioritize speed and simplicity, MIG welding is your go-to. But if you value precision, aesthetics, and control, TIG welding is the clear winner.
So, whether you’re a hobbyist, a professional, or somewhere in between, understanding the differences between these two welding methods will help you make an informed decision and achieve the best results for your projects.
Ready to dive into welding? Start with MIG if you’re just beginning, but don’t shy away from exploring TIG as your skills grow. Happy welding! 😊
Note: Always prioritize safety when welding. Wear proper protective gear, ensure adequate ventilation, and follow all safety protocols.
TIG vs MIG Welding for Aluminum Alloys
Is TIG welding better than MIG welding?
It depends on the application! TIG excels in precision welding for thin sheets (e.g., aerospace components), while MIG is ideal for high-speed production of medium-thick plates (e.g., automotive frames).
Which welding type is harder to master, TIG or MIG?
TIG welding is more challenging due to its demand for hand-foot coordination and precise heat control, while MIG focuses on parameter optimization for consistent results.
Can a MIG welder weld stainless steel?
Yes! Use a tri-gas mix (He/Ar/CO₂) and stainless-specific wires (e.g., ER308L) to prevent oxidation and ensure corrosion resistance.