That satisfying whirr of a well-tuned lathe, the clean shaving of steel peeling away under a sharp cutter, the final part sliding perfectly into place with micron-level precision – this is the magic of machining. But behind every perfect cut and flawless fit lies a foundation of essential machinist tools. Whether you’re a weekend hobbyist building a model engine, a maker crafting custom motorcycle parts, or a seasoned pro setting up a new shop, having the right tools isn’t just convenient – it’s the difference between frustration and triumph, between wasted material and masterpiece, between safety and hazard.
Feeling overwhelmed? Wondering where to start or if your workshop is truly complete? Stop guessing. This definitive 2025 checklist breaks down the must-have machinist tools into logical categories, covering everything from the absolute basics to precision-enhancing upgrades. We’ll prioritize based on need and budget, offering practical pro-tips along the way. Bookmark this guide – it’s your roadmap to a workshop built for precision and success.
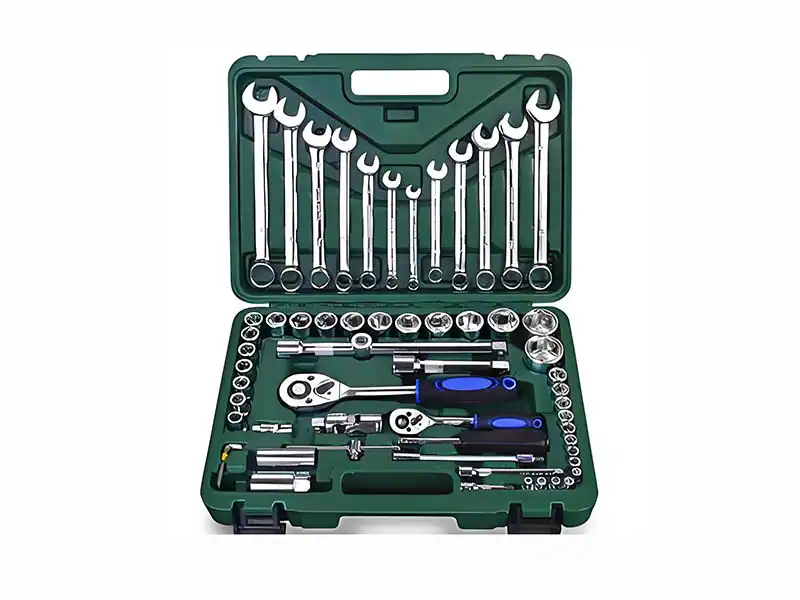
I. The Bedrock of Accuracy: Measurement & Layout Tools (Measure Twice, Cut Once!)
Precision machining starts with precise measurement. Without accurate data, even the best cuts are just guesses. This category is non-negotiable for any level of machining work.
- Calipers (Digital, Dial, or Vernier): Your #1 Essential Tool. Used constantly for measuring Outside Diameters (OD), Inside Diameters (ID), depths, and step heights. Digital calipers offer quick readings; dials provide excellent tactile feel; verniers are durable but slower. Aim for at least 0.001″ (0.02mm) resolution/accuracy. *Pro Tip: Start with a good 0-6″ digital caliper – it’s the workhorse.*
- Micrometers (Outside): For critical high-precision measurements where calipers aren’t enough. Essential for checking shafts, pins, and tolerances below 0.001″. You’ll need them in size ranges (e.g., 0-1″, 1-2″). Digital or analog (ratchet thimble) are common. *Pro Tip: A 0-1″ mic is often the first and most used.*
- Combination Square: Incredibly versatile. Use it for checking 90° & 45° angles, scribing lines, measuring depths, setting heights on a surface plate, and as a small precision straight edge. Quality matters – a flimsy square is worthless. Pro Tip: Look for a hardened steel blade and a solid, square head.
- Precision Steel Rules/Scales: Rigid, ground-steel rulers (6″, 12″, 18″) for direct measurement, layout work, and checking flatness as a straight edge. Avoid flexible tape measures for precision work. Pro Tip: Get a 6″ and 12″ rule with clear, fine graduations.
- Scribers & Surface Gauge: Used together for precise layout lines on metal surfaces. The scriber scratches the line; the surface gauge sets the height accurately, often used on a surface plate. Pro Tip: A basic surface gauge is a huge upgrade over hand-scribing.
- Machinist Squares (Precision Squares): Small, ultra-accurate squares (e.g., 1″, 2″, 4″) for verifying perpendicularity and checking the squareness of setups, tools, and small parts. Crucially different from carpentry squares! Pro Tip: A 4″ precision square is incredibly useful.
- Center Punches: Create a small starter dimple to accurately locate drill bits, preventing walking. A sharp, properly ground punch is key. Pro Tip: Use a sharp blow with a small hammer.
- Pro Advice: Invest heavily here first. Calipers and a good combination square are your foundation. Learn to use them correctly and keep them clean and protected. Consider a small granite surface plate (e.g., 9″x12″) as a future upgrade for serious layout work.
II. Shaping Metal: Cutting, Forming & Finishing Tools (Making the Cut)
These are the tools that directly remove metal, create shapes, add threads, and clean up edges. They turn measurement into reality.
- Files (Assorted Shapes & Cuts):Essential for hand finishing, deburring, shaping, and fitting. You need a variety:
- Cuts: Bastard (coarse), Mill (medium), Smooth (fine).
- Shapes: Flat, Half-Round, Round, Square, Triangular (for corners).
- Pro Tip: Buy quality (e.g., Nicholson, Grobet). Start with flat bastard, mill, and smooth; half-round bastard; and a small smooth round file.
- Hacksaw & Quality Blades: For manual cutting of stock, bar, and tube. A rigid frame is crucial. Select blades based on Teeth Per Inch (TPI): Higher TPI (18-24) for thin metal/thin wall tube, lower TPI (14-18) for thicker stock. Pro Tip: Buy name-brand bi-metal blades (e.g., Starrett, Lenox) – they last much longer.
- Chisels (Cold Chisels): For cutting, chipping, and removing material, especially useful for cast iron or where power tools can’t reach. Flat and cape styles are common. Pro Tip: Keep them sharp! A dull chisel is dangerous.
- Hammers (Ball Peen, Soft Face): Driving chisels, punches, and light forming. Ball peen (machinist’s hammer) is standard. Soft-face hammers (brass, copper, plastic, deadblow) are vital for assembly without marring surfaces. Pro Tip: A 16oz ball peen and a medium deadblow are versatile starters.
- Taps & Dies (Sets): Creating internal (taps) and external (dies) threads. Buy sets covering common sizes in your needed standards (Metric, UNC, UNF). Quality matters immensely to avoid broken taps! Pro Tip: ALWAYS use appropriate cutting fluid. Start with a basic metric and SAE set.
- Deburring Tools: Crucial for safety and finish. Quickly removes sharp edges (burrs) left by cutting or machining operations. Handheld models with replaceable blades are efficient. Pro Tip: Don’t skip this! Burrs cause cuts and interfere with fits.
- Pro Advice: ALWAYS wear safety glasses when using any cutting tool! Sharp tools are safer and more effective than dull ones. Invest in a good tap wrench (see Section VI).
III. Holding It All Together: Workholding & Fastening Tools (Secure Your Work!)
Precision and safety demand rock-solid workholding and the right tools for assembly. Your workpiece must be immovable.
- Bench Vise (Heavy Duty):The cornerstone of your workbench. This is your “third hand.” Prioritize:
- Size: 4″ to 6″ jaws are common for home shops.
- Mounting: Bolt it securely to a VERY sturdy bench.
- Jaws: Hardened steel jaws are standard; have soft jaws (copper, aluminum, plastic) to protect finished parts.
- Swivel Base: Very useful but adds cost. Pro Tip: DO NOT SKIMP HERE. Buy the heaviest, highest quality vise you can afford (e.g., Wilton, Yost). It’s a lifetime investment.
- C-Clamps (Various Sizes): Versatile clamping for welding, assembly, fixturing, or holding odd shapes. Get a range (2″, 4″, 6″, 8″). Pro Tip: Parallel clamps offer more stability but C-clamps are essential.
- Parallels: Hardened steel bars used in pairs to support workpieces level and parallel in a vise or on a machine table. Essential for milling and accurate drilling. *Pro Tip: A set of 1/2″ x 6″ parallels is a great start.*
- Wrenches: Focus on:
- Hex Keys (Allen Wrenches – L-keys & T-handles): PARAMOUNT for machine screws. Buy high-quality, hardened sets (metric & SAE). Ball-ends are convenient.
- Combination Wrenches (Open End/Box End): For larger nuts/bolts.
- Adjustable Wrench: Use SPARINGLY and with caution – they easily damage precision fasteners. Pro Tip: Invest in good hex keys (e.g., Bondhus, Wera).
- Screwdrivers (Precision & Standard): Quality tips are crucial to avoid cam-out and damaging screw heads. Have a range of sizes in flathead and Phillips (especially #1, #2, #3). Precision sets handle small screws. Pro Tip: Look for hardened tips and comfortable grips.
- Punches (Pin Punches, Starter Punches): For driving pins, aligning holes, and starting bearing/sleeve removal. Different diameters are needed. Pro Tip: Keep punches properly ground and avoid mushroomed heads.
- Pro Advice: Your vise is the heart of manual workholding. Parallels are indispensable for milling. Never use an adjustable wrench on a precision fastener if you can avoid it – use the correct sized wrench or socket.
IV. Powering Up: Core Workshop Machinery (Level Up Your Capability)
These machines dramatically expand your capabilities, efficiency, and the types of projects you can tackle. Investment increases significantly here.
- Drill Press: Essential for accurate, perpendicular holes. Far superior to hand drills for precision and consistency. Key features: Quill travel, table rigidity, chuck quality (keyed or keyless), and horsepower. Pro Tip: Often the first “real” machine purchase for home shops. Look for a sturdy floor or bench model.
- Bench Grinder: Sharpening drills, lathe tools, chisels, and deburring. Usually 6″ or 8″ wheels. Vital features: Sturdy construction, adjustable tool rests, eye shields, and spark guards. Pro Tip: Get a quality grinder (e.g., Baldor, Jet) and learn to dress wheels. ALWAYS use eye protection!
- Bandsaw (Vertical or Horizontal): Crucial for efficient stock cutting. Cuts curves, straight lines, and miters. Saves immense time and material vs. hacksaws. Vertical is more versatile for shapes; horizontal excels at straight cuts for stock prep. Pro Tip: A good bandsaw is transformative. Even a small vertical model is hugely valuable.
- Angle Grinder:Versatile powerhouse for cutting, grinding, sanding (with flap discs), and wire brushing. 4.5″ is the most common size. STRONG SAFETY WARNING:
- Always use the guard.
- Use the correct disc for the job (cutting vs. grinding).
- Secure the workpiece – NEVER hold it by hand.
- Wear a face shield and safety glasses, hearing protection, and gloves. Pro Tip: Invaluable, but respect its power. Consider a variable speed model.
- Lathe ($$$$): The heart of turning operations. For creating cylindrical parts, facing, boring, threading, and more. Benchtop models suit smaller work; larger floor models offer more capacity/power. Pro Tip: A major investment. Research heavily (size, swing, bed length, features) before buying.
- Milling Machine ($$$$): The ultimate shaping tool. For machining flat surfaces, slots, gears, holes, and complex contours. Benchtop mills (e.g., mini-mills) are entry points; knee mills offer more capability. Pro Tip: Often paired with a lathe. Requires significant investment and learning.
- Pro Advice: Start with a drill press and bench grinder. A bandsaw is a massive efficiency boost. Lathes and Mills are significant commitments – ensure you have the space, budget, and project need before diving in. Reinforced: Angle Grinder Safety is NON-NEGOTIABLE.
V. Precision & Protection: The Supporting Cast (The Finishing Touches & Non-Negotiables)
These tools elevate your precision on machines and ensure you stay safe. Safety Gear is MANDATORY.
- Dial Indicator & Magnetic Base ($$): Vital for precision machining. Measures runout (wobble), aligns workpieces perfectly in lathe chucks or mill vises, sets tools to exact heights, and checks part dimensions. The magnetic base holds it securely to machine surfaces. *Pro Tip: Unlocks true precision. A 0.001″ resolution indicator and a good Noga-type base are worth it.*
- Edge Finder & Center Finder: Essential accessories for milling machines and drill presses to accurately locate the edge or center of a workpiece before machining. Pro Tip: A wiggler edge finder is inexpensive and effective.
- Machinist Level (Precision): Used for accurately leveling lathes, milling machines, and surface plates. Much more precise than a carpenter’s level. Pro Tip: Necessary for proper machine setup.
- Tap Wrench (T-handle): The proper tool for comfortable and controlled hand tapping. Provides better feel and reduces tap breakage compared to adjustable wrenches. Pro Tip: Get a good quality T-handle wrench.
- Cutting Fluid & Lubricants: Extend tool life dramatically, improve surface finish, reduce heat, and help evacuate chips. Essential for drilling, tapping, turning, and milling. Types include oils, soluble oils, and synthetics. Pro Tip: Don’t machine dry! Use the right fluid for the material and operation.
- SAFETY GEAR (PPE): Safety First! Mandatory Personal Protective Equipment
- Safety Glasses / Goggles (ANSI Z87.1+): ALWAYS ON in the workshop. Impact-rated for flying chips and debris. Goggles offer better splash/chemical protection.
- Hearing Protection (Ear Muffs/Plugs): Essential when operating machinery, grinders, or air tools. Prevent long-term hearing damage.
- Respirator/Dust Mask: Needed for grinding, sanding, working with composites, or exposure to fumes/oil mist. Use N95/P100 masks or respirators with appropriate cartridges.
- Shop Apron / Protective Clothing: Sturdy cotton or leather apron protects against sharp chips, cutting fluids, and sparks. Avoid loose clothing or jewelry.
- Sturdy Work Boots (Steel/Composite Toe Recommended): Protect feet from heavy dropped objects and sharp metal on the floor.
- Pro Advice: A dial indicator setup is essential for serious work on lathes or mills. PPE IS NOT OPTIONAL OR “SOMETIMES” – IT’S EVERY SINGLE TIME YOU STEP INTO THE SHOP. Neglecting safety can have permanent consequences.
VI. Smart Workshop Practices: Care, Budget & Growth (Beyond the Tools)
Building a great workshop is a journey, not a single purchase. Smart habits ensure longevity and continuous improvement.
- Tool Maintenance is King:
- Cleanliness: Wipe down tools after use, especially measuring instruments. Remove cutting fluids and chips.
- Lubrication: Lightly oil precision tools and bare metal surfaces to prevent rust (e.g., use way oil, light machine oil, or specific rust preventatives).
- Calibration: Periodically check critical measuring tools (calipers, mics) against known standards. More critical for pros, but good practice for all.
- Proper Storage: Use toolboxes, cabinets, shadow boards, or pegboard. Keep tools organized and protected from damage and environmental hazards. Avoid moisture!
- Sharpening is Crucial: Dull tools are dangerous, inefficient, and produce poor results. Regularly sharpen:
- Drill Bits (using a drill doctor or bench grinder technique)
- Lathe Cutting Tools (tool bit grinders)
- Milling Cutters (specialized equipment or send out)
- Chisels & Punches (bench grinder)
- Files (Clean with file card; they wear out and need replacement eventually).
- Workshop Organization: A cluttered shop is an inefficient and unsafe shop. Invest time in:
- Labeling drawers and bins.
- Using shadow boards for frequently used tools.
- Implementing a logical storage system.
- Keeping walkways clear.
- Strategic Acquisition:
- Prioritize: Start with the core measurement, workholding, and hand tools outlined in Sections I-III. Add power tools and machines (Section IV) as your skills and projects demand them. Don’t buy a Bridgeport before you have good calipers!
- Budget Wisely:Quality over quantity for core tools. It’s better to have one excellent micrometer than three poor ones. For machines, consider:
- New: Warranties, latest features.
- Used Industrial: Often fantastic value (vises, machinery) but requires inspection skills. Check for wear, damage, and completeness.
- Brand Awareness: While budget dictates, be aware of brands known for machinist quality (Starrett, Mitutoyo, Brown & Sharpe, SPI, Noga, Mitty, Kennedys tool boxes, Walter, Armstrong files, etc.). They represent reliability and precision, even if acquired slowly.
- Continuous Learning: Machining is a deep skill.
- Books: Classic texts like “Machine Shop Practice” (K.H. Moltrecht).
- Online Forums: Practical Machinist, hobbyist forums, Reddit (r/Machinists).
- YouTube Channels: Many excellent machinists share knowledge (e.g., This Old Tony, Abom79, Joe Pieczynski, Blondihacks, NYC CNC).
- Local Makerspaces: Access to larger equipment and community knowledge.
Your Journey Starts Now
Equipping your dream workshop takes time, planning, and smart investment. This ultimate checklist provides the blueprint. Start by mastering the fundamentals – precision measurement, secure workholding, and essential hand tools. Prioritize safety above all else. Add machinery strategically as your needs grow. Maintain your tools diligently, stay organized, and never stop learning.
Remember, every seasoned machinist started somewhere. Focus on building a solid foundation with quality core tools. With this checklist in hand, you’re well on your way to transforming your workshop into a space where precision thrives, projects succeed, and the satisfaction of creating something tangible becomes a regular occurrence. Now go build something amazing!