Introduction
This article covers die casting technology and its applications.
You will learn about:
- What is die casting?
- How Die Casting Works
- Different Die Casting Processes Explained
- Comparing metals for die casting
- FAQ Section
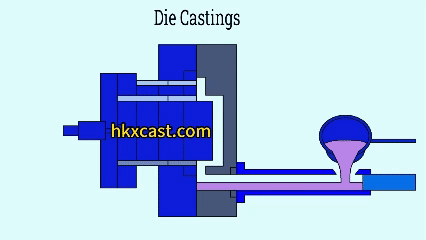
What Is Die Casting?
Die casting is a metal casting process. It works by melting metal and forcing it into a mold under high pressure and speed. The metal cools and hardens, then the mold opens, and the finished part is pushed out.
Parts made with this method have a smooth surface finish (Ra 3.2 to 6.3 μm) and precise dimensions (Grade T11 to T13).
Common metals used include aluminum, zinc, magnesium, lead, and tin.
Depending on the metal, the process is called:
- Aluminum die casting (for aluminum parts)
- Zinc die casting (for zinc parts)
- Magnesium die casting (for magnesium parts)
…and so on.
This method is ideal for mass production due to its high efficiency and consistency.

How Die Casting Works ?
1.Mold Preparation
Each product has its own unique shape and structure. When designing a mold, key considerations include the number of cavities and the required press tonnage.
Based on the product layout, molds can be categorized into:
Single-cavity mold: The simplest type, producing only one product per casting cycle.
Multi-cavity mold: More complex than single-cavity molds, with variations like double-cavity, triple-cavity, etc. Each cycle produces multiple identical products, making it ideal for high-volume production.
Unit mold : Contains at least two different product types, producing one of each per cycle. Often used for matching product sets.
Combination mold: A hybrid of family and multi-cavity molds, capable of producing multiple products (same or different types) in a single cycle. Suitable for mixed-quantity or large-scale production.
Under the same press tonnage:
Multi-cavity mold cost > Single-cavity mold cost
Multi-cavity product cost < Single-cavity product cost
Multi-cavity mold cost < (Single-cavity mold cost × 2)
After manufacturing, molds must be cleaned, oiled, and treated for rust prevention to avoid corrosion, ensuring product accuracy and mold longevity. Before each production run, inspection and preheating are required. Periodic heat treatment after a certain production volume helps extend mold life and reduce cracking risks.
2.Metal Melting
In die casting, commonly used metals include aluminum, zinc, magnesium, and copper alloys. These metals are solid at room temperature and must be heated in a furnace until melted before being injected into molds.

3.Injection Process
The injection method depends on the type of die casting machine:
- Cold Chamber Machine
The injection chamber is separate from the melting furnace. Liquid metal is poured into the chamber before injection. - Hot Chamber Machine
The injection chamber is submerged in molten metal inside a heated pot. The injection mechanism is mounted on the pot, not directly on the machine.
4.Cooling & Solidification
The molten metal cools and hardens inside the mold. Cooling time varies (seconds to minutes) based on part size and thickness. Pressure is maintained during cooling to improve density, prevent shrinkage, and reduce air pockets.
5.Ejection
After solidification, the mold opens, and the part is pushed out using ejector pins or plates. The part must fully harden before ejection to avoid deformation or damage.
6.Post-Processing
After casting, the part is trimmed to remove flaws like burrs or scratches. Additional steps (cutting, drilling, or surface finishing) may be needed to meet design specs. Finally, Surface treatments can enhance strength and appearance.
Different Die Casting Processes Explained
Gravity Die Casting
Gravity casting uses natural gravity to fill molds, saving energy and reducing waste. It works well for thick, sturdy parts like engine blocks and cylinder heads in cars. The slow filling process means fewer air bubbles, making the final product strong and precise.
Pressure Die Casting
Pressure die casting forces metal into the mold under pressure. It has two main types:
- Low-Pressure Casting
- Gentle pressure fills molds smoothly, creating parts with clean surfaces and few flaws. Perfect for car fuel systems or parts that need to stay sealed.
- High-Pressure Casting
- High pressure fills molds in seconds, great for thin, detailed parts like phone cases or car trim. Ideal for making lots of parts quickly.
Vacuum Die Casting
Uses a vacuum to remove air bubbles, giving parts a smooth finish. Used for medical tools (like bone implants) and airplane parts that must work perfectly under pressure.
Squeeze Die Casting
Combines pressure and special cooling to make metal tougher. Used for car parts like suspension arms or brakes that need to last long and handle heavy stress.
Semi-Solid Die Casting
Molds metal that’s part solid, part liquid to create thin, intricate designs. Used for lightweight electronics (like laptop frames) and car parts needing both detail and strength.
Die Casting Pros and Cons
Die casting is a widely used metal forming process known for its efficiency, precision, and suitability for mass production. However, like any manufacturing method, it comes with its own set of advantages and limitations. The table below outlines some of the key pros and cons to consider when selecting die casting for a particular application:
S/N | Advantages | Disadvantages |
---|---|---|
1 | Provides high production speed, making it suitable for mass manufacturing. | Tooling and die costs are high, especially during initial setup. |
2 | Enables accurate production of thin-walled and complex parts with high dimensional stability. | Large or bulky parts are difficult to cast due to size and pressure limitations. |
3 | Produces parts with excellent strength and a refined grain structure. | Not suitable for ferrous metals or alloys with very high melting temperatures. |
4 | Offers cost-effective production for high-volume runs, reducing unit cost significantly. | Risk of air entrapment during casting, potentially causing internal porosity in final products. |
5 | Results in parts with smooth surfaces, reducing the need for extensive post-processing operations. | Production cycle time may be longer for complex designs or when using special casting techniques. |

Comparing metals for die casting
Main Die Cast Alloys | Casting Temperature | Key Features |
---|---|---|
Aluminum Alloy | 650~680°C | 1. Light weight – good for parts needing less mass 2. Strong yet flexible 3. Resists rust and corrosion well |
Zinc Alloy | 420~440°C | 1. Casts well – makes complex shapes precisely 2. Very strong and hard, with good toughness 3. Easy to finish surfaces 4. Fast production |
Magnesium Alloy | 640~680°C | 1. Very light but strong 2. Flows easily when melted 3. Reduces vibration and blocks magnetism |
Lead-Tin Alloy | Around 200°C | 1. Melts easily, flows well, doesn’t shrink much 2. Easy to shape 3. Smooth finish, easy to coat |
Copper Alloy | 900~980°C | High melting point wears out molds fast – use less often |

5 Advantages of Die Casting Technology
Die casting is widely recognized in engineering and manufacturing for its precision, repeatability, and cost-efficiency in producing metal components. Below are five well-established advantages of die casting technology, supported by real-world industrial application insights:
1. Complex Thin-Walled Parts
Die casting excels at producing geometrically complex components with thin walls and tight corners that would be difficult or impossible with other metal forming methods like sand casting or machining. The high-pressure injection fills fine cavities in the mold, enabling intricate internal features such as ribs, bosses, and threads—all in a single operation.
2. High Mechanical Properties
Because molten metal is rapidly injected and cooled in a controlled die, the resulting microstructure is often fine-grained and uniform. This improves tensile strength, hardness, and fatigue resistance—critical for load-bearing components such as transmission housings, suspension arms, and industrial enclosures.
3. High Dimensional Tolerance
Die casting achieves excellent dimensional accuracy, typically within ±0.1 mm depending on the part size and alloy used. This reduces the need for secondary machining or finishing, allowing parts to be used as-cast or with minimal post-processing—especially beneficial in automotive, aerospace, and precision instrumentation sectors.
4. Smooth Surface Finish
Die cast surfaces typically range from 1.6 to 6.3 μm Ra in surface roughness, depending on mold condition and casting parameters. This is sufficient for cosmetic components and those requiring coating or painting. Smooth surfaces also improve sealing performance in parts like pump housings or hydraulic components.
5. Cost-Effective for Mass Production
While the initial investment in dies and equipment is high, die casting becomes economically advantageous at medium to high production volumes. Cycle times are short (often under 60 seconds), and automation is easily integrated. This makes it ideal for industries requiring tens of thousands—or millions—of consistent, high-quality parts.
Choose HKX for Your Custom Die Casting Parts
Looking for a reliable die casting partner? HKX offers ISO 9001:2015-certified manufacturing, with experienced engineers, precise tooling, and fast turnaround for high-volume or custom parts. We support a wide range of alloys, offer multiple surface finishes, and provide instant online quotes with free DfM feedback. Trusted by engineers across industries, HKX ensures quality, efficiency, and full production visibility—helping you reduce lead time and cost.
👉 Get a quote from HKX today and streamline your die casting project.
FAQ Section
1. What metals are used in die casting?
Common metals include aluminum, zinc, magnesium, and copper alloys.
2. Is die casting expensive?
Initial tooling costs are high, but per-unit costs drop significantly in mass production.
3. What’s the difference between hot and cold chamber die casting?
Hot chamber is for low-melting metals (zinc, magnesium), while cold chamber handles high-melting metals (aluminum, copper).
4. Can die casting be used for small parts?
Yes, die casting is excellent for small, intricate components like electronics connectors.
5. How long does a die casting mold last?
A well-maintained die can last 100,000 to 1,000,000+ cycles, depending on material and usage.